AUTUMN 2021 - INSPIRE
THE PAPER THAT INSPIRED THE MAZDA MX-30 INTERIOR
AUTUMN 2021 - INSPIRE
THE PAPER THAT INSPIRED THE MAZDA MX-30 INTERIOR
"To make consistently beautiful washi day after day is very hard. To make 'perfect' washi requires many years of practice and routine."
CRAIG ANCZELOWITZ, AWAGMI
"To make consistently beautiful washi day after day is very hard. To make 'perfect' washi requires many years of practice and routine."
CRAIG ANCZELOWITZ, AWAGMI
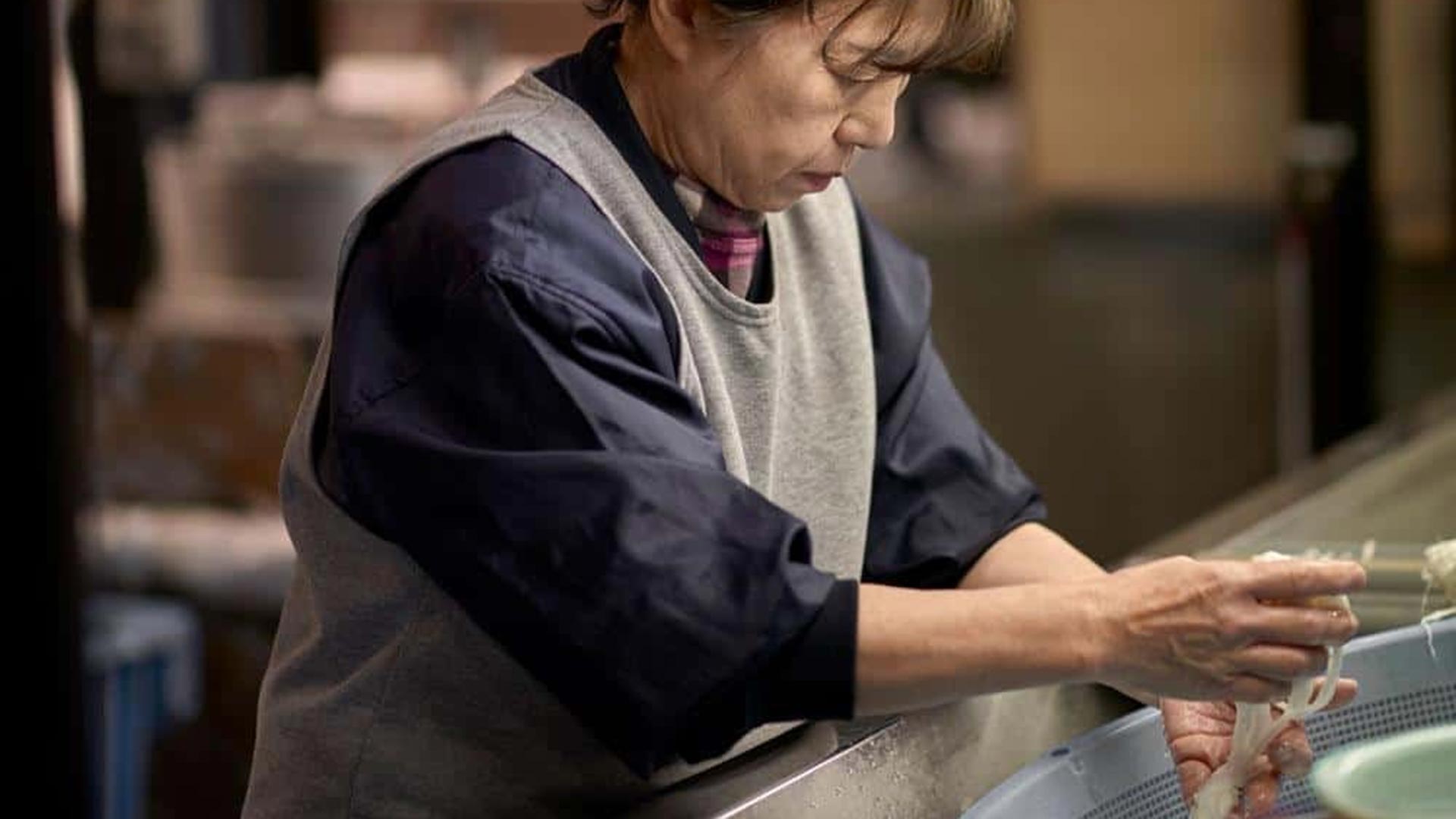
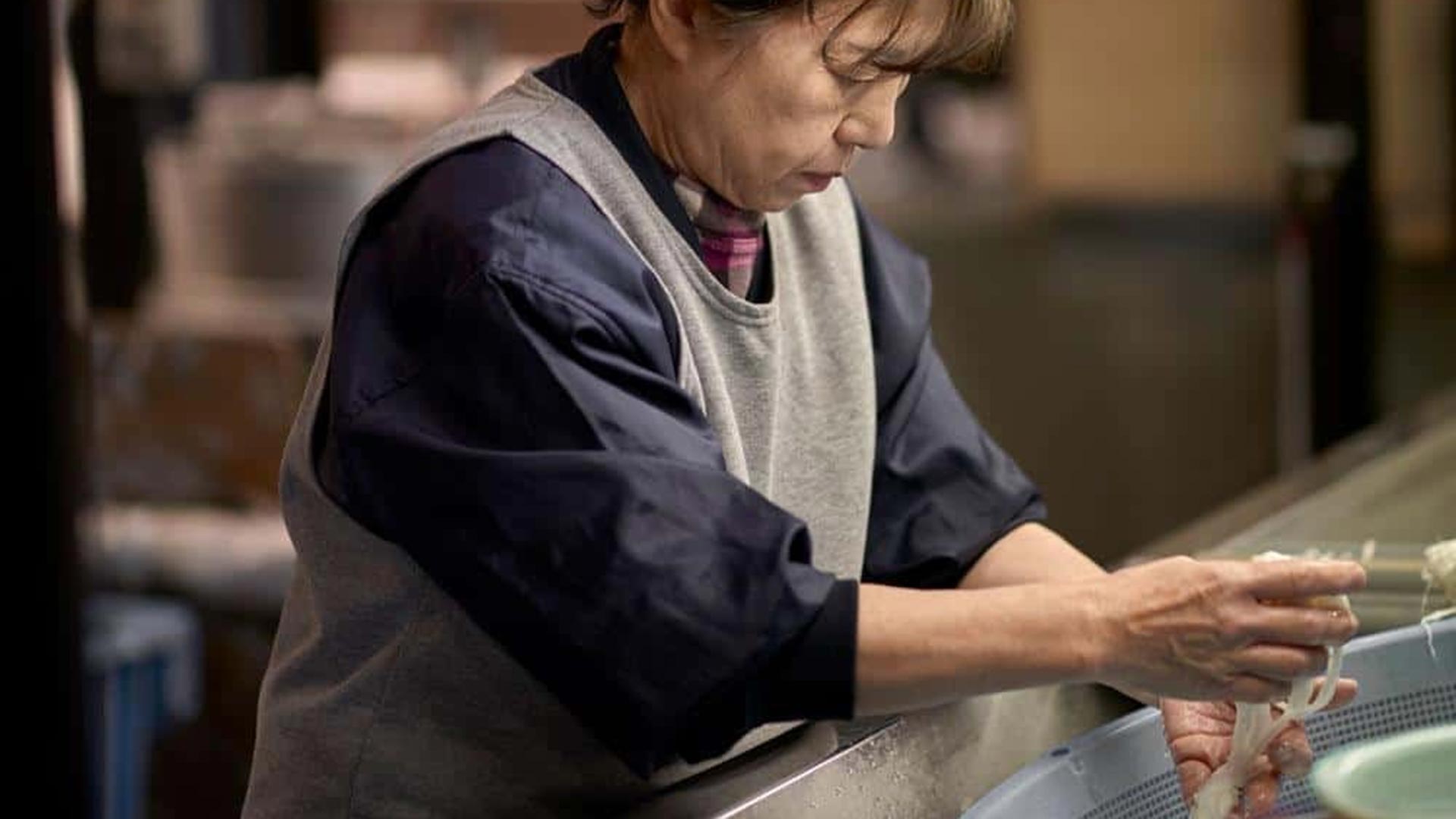
How to make it
Washi is most commonly made using the nagashisuki method, developed around 1,000 years ago. The plants that comprise the paper’s ingredients are normally harvested during the winter months. The branches are steamed to soften the bark so it can be stripped away and dried. This dry bark is then boiled to create a pulpy substance and beaten by hand to loosen the fibres. The pulp mixture is scooped up and put onto a bamboo screen, and a viscous neri solution is added to the vat in order to get an even dispersal of the mixture. This mixture is rocked back and forth and side to side repeatedly so longer fibres are created and tightly interwoven. The flexible screen is removed from the mould with the wet sheet of paper still attached. The papermaker uses the screen to place the fresh wet sheet on the stack of newly formed sheets, which is left to dry. Finally, the paper is pressed to remove excess water, after which sheets are separated and brushed to remove any invasive textures and left again to complete the drying process.
How to make it
Washi is most commonly made using the nagashisuki method, developed around 1,000 years ago. The plants that comprise the paper’s ingredients are normally harvested during the winter months. The branches are steamed to soften the bark so it can be stripped away and dried. This dry bark is then boiled to create a pulpy substance and beaten by hand to loosen the fibres. The pulp mixture is scooped up and put onto a bamboo screen, and a viscous neri solution is added to the vat in order to get an even dispersal of the mixture. This mixture is rocked back and forth and side to side repeatedly so longer fibres are created and tightly interwoven. The flexible screen is removed from the mould with the wet sheet of paper still attached. The papermaker uses the screen to place the fresh wet sheet on the stack of newly formed sheets, which is left to dry. Finally, the paper is pressed to remove excess water, after which sheets are separated and brushed to remove any invasive textures and left again to complete the drying process.